
Raw Material
It is mainly suitable for crushed hard plastic waste, includes HDPE, LDPE, PP, ABS and other. This pelletizing line can also deal with light soft waste, including crushed PE film waste, PP silk material, PP / PE woven bag, PE foamed material, etc. They can be sent to the extrusion section by a pressure feeding device to melt and mix.
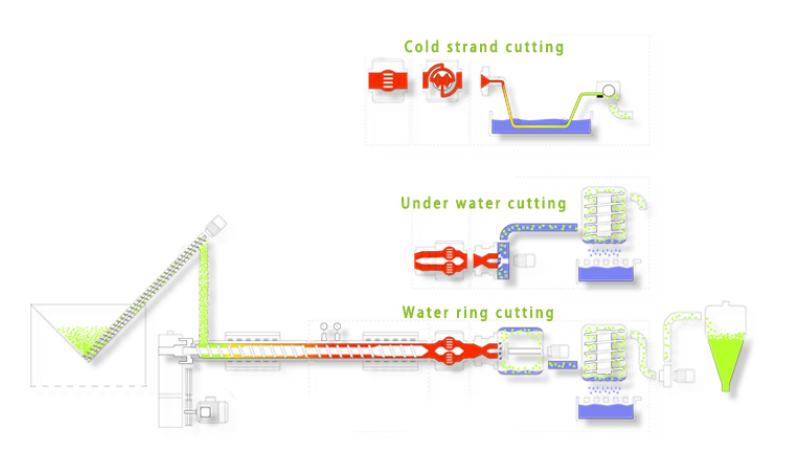
The advantages of core components
1.The barrel of the granulator is manufactured by 45 # forged steel inserted alloy sleeve (or the whole 38CrMoAlA nitride), which is friction and erosion-resistant. 2.The screw is made of alloy steel, have passed by vacuum quenching or nitride, it is durable. 3.The gearbox output shaft bearing uses German INA bearings, the spindle is made of special alloy materials, which has been carburized, ensuring high-efficiency and long-term stable operation. 4.The heater is made of cast aluminum or cast copper electric heater, equipped with an insulation module, energy saving and durable. 5.Japanese RKC dual-channel PID digital smart temperature control meter, INVT constant torque AC inverter, vacuum exhaust unit, soft water cooling system on barrel, stainless steel water tank, dryer, granulator, electrical control cabinet, etc. 6.The granulation equipment can also be equipped with large flow plate screen changer with double working position, a mobile hydraulic station, different granulated auxiliary machine can be set according to different materials, constituting different granulation lines, as shown below:
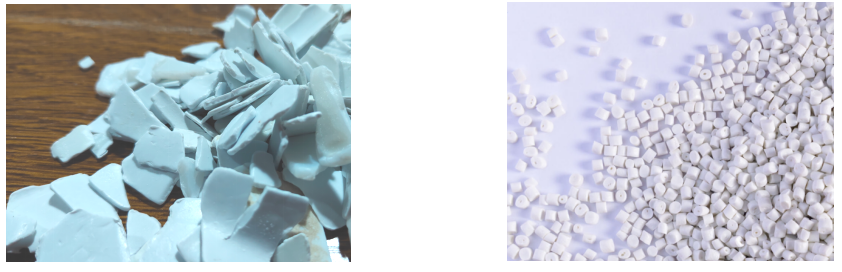
Model | PTC30 | PTC45 | PTC65 | PTC90 | PTC100 |
diameter (mm) | 30 | 45 | 65 | 90 | 100 |
L/D | 18-42 | ||||
Speed (rpm) | 10-150 | ||||
Output (kg/hr) | 2-40 | 10-60 | 100-150 | 150-220 | 220-320 |
Model | PTC120 | PTC150 | PTC160 | PTC180 | PTC200 |
diameter (mm) | 120 | 150 | 160 | 180 | 200 |
l/d | 18-42 | ||||
Speed (rpm) | 10-150 | ||||
Output (kg/hr) | 300-400 | 400-550 | 600-700 | 700-900 | 1000-1300 |
PolytecModel | PTCS | ||
Final product | Plastic granules | ||
Structure | Feeding hopper, extruder, mould, cold water tank, dryer, pelletizer, silo | ||
Raw materials | HDPE,LDPE,LLDPE, PP, BOPP, PA, PC, PS, PU, EPS,ABS | ||
Output | 100kg~ 1200 kg/hr | ||
Fending system | Rigid materials can be fed directly(For processing light thin films, the force feeder can be installed) | ||
Screw diameter | 65~180mm (customized) | ||
L/D | 30/1,32/1,34/1,36/1 (customized) | ||
Screw material | 38CrMoAl | ||
Degassing hole | Double degassing hole, single degassing hole or no degassing hole (customized) | ||
Granulation method | Air cooling die face pelletizer or water cooling strand cutter | ||
Cooling method | Water cooling | ||
Voltage | Customized (Example: America 480V 60Hz, Mexico 440V / 220V 60HZ, Saudi Arabia 380V 60Hz, Nigeria 415V 50Hz) | ||
Optional accessories | Metal detector (S+S), conveyor belt, screw loader, forced feeder | ||
Delivery day | 60 days | ||
Warranty | One year | ||
Technical support | Engineers available to service machinery overseas | ||
PolytecModel | PTCS | ||
Product | Plastic Pellets | ||
Recycling Machine Structure | Feeding hopper, extruder, stretch die, cold water tank, dryer, pelletizer, silo | ||
Recycled Material | HDPE,LDPE,LLDPE, PP, BOPP, PA, PC, PS, PU, EPS,ABS | ||
Production Range | 100kg~ 1200 kg/hr | ||
Feeding System | Direct hopper feeding of heavy and hard return materials (for processing light film sheets, a forced feeder can be installed) | ||
Screw Diameter | 65~180mm (Customized) | ||
Screw length to diameter ratio | 30/1,32/1,34/1,36/1 (Customized) | ||
Screw material | 38 chromium molybdenum aluminum | ||
Degassing hole | Single exhaust or double exhaust, no exhaust for non-printed film (customized) | ||
Granulation Method | Die face hot cutting or strand cutting | ||
Cooling Method | Water cooling | ||
Voltage | Customized (for example: USA 480V 60Hz, Mexico 440V/220V 60Hz, Saudi Arabia 380V 60Hz, Nigeria 415V 50Hz...) | ||
Options | Metal detector (S+S), conveyor belt, screw feeder, forced feeder | ||
Delivery date | 60 days | ||
Warranty | 1 year | ||
Technical Support | Installation and commissioning training |
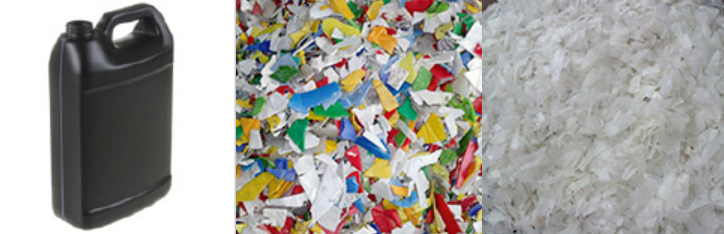
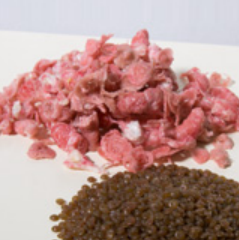



Details
Feeding structure
Material can be directly added to the extrusion section through a screw feeding device (or a conveyor belt feeding device). The feeding speed is automatically adjusted by detecting the load of the extruder motor and controlling the current ampere load to prevent excessive feeding or insufficient feed.
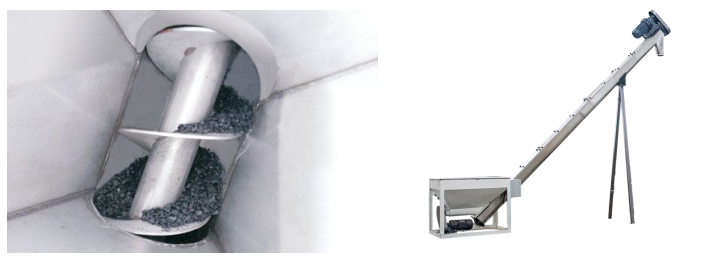
Extruder
It consists of a gear reducer (high torque, low noise, external cooling cycle system), a nitriding 38CrMoA1 screw, a barrel (38CrMoAlA, nitriding, controlled by temperature control ), and a vacuum system.
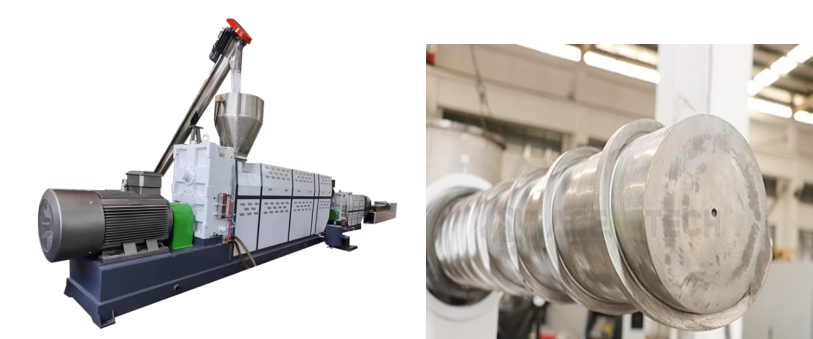
Melt filter screen changer system
Suitable easy-to-operate filtration systems can be selected according to the condition of the raw material, and the dirt is filtered to ensure the pureness of the final pellets. Optional: a.Laser screen changer - automatic scraping technology, can effectively reduce the frequency of cleaning and replacement; b.Backflush screen changer - automatic cleaning mesh, greatly reducing the frequency of the filter replacement, reducing labor; c.Double-piston large-scale screen changer - larger filter area, automatic and hydraulic; d.Plate screen changer - easily operate, screen filter can be recycled, save cost, suitable for crude filtration and fine filtration.
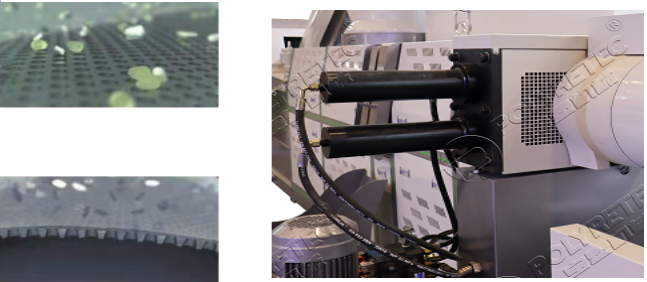
Laser screen changer(optional for HDPE/PP/ABS/PS regrinds 100micron)
Applications
PTJ continuous melt filters are suitable for processing all standard polyolefins and polystyrenes with the exception of PVC、PVDC、EVA; they are designed to remove foreign particles such as paper, aluminum, wood, elastomers (rubber, silicone) or high-melting polymer composites from heavily contaminated materials.
Examples
Processing material | contamination | Contamination by weight % | Filtration fineness | Waste contamination% | Material losses % |
PE | paper | 5 | 30-120mesh | 58-67 | 3-4 |
PPHDPE | PET | 4 | 57-66 | 2-3 | |
PS | aluminum | 3-4 | 57-60 | 2-3 | |
PP | rubber, silicone | 2-3 | 55-60 | 1-2 | |
PE、PP | composite | 0.5 | 55-65 | 0.3-0.4 |
Technical data
model | PTJ300 | PTJ400-D | PTJ500-D |
Filter diameter in mm | 1X300mm | 2X400mm | 2X500mm |
Filter area in cm2 | 575cm² | 2112cm² | 3472cm² |
Filtration fineness | 120-600μm 30-120Mesh | ||
Maximum operating pressure in bar | 250bar | 250bar | 250bar |
Number of heating zones | 4 | 5 | 6 |
Installed heating capacity in KW | 12 | 28 | 42 |
Engine power in KW | 3.0 | 5.5 | 11.0 |
Motor power discharge screw in KW | 1.5 | 2X1.5 | 2X2.2 |
Throughput capacity in kg/h | 300-500Kg | 500-1200Kg | 1000-2000Kg |
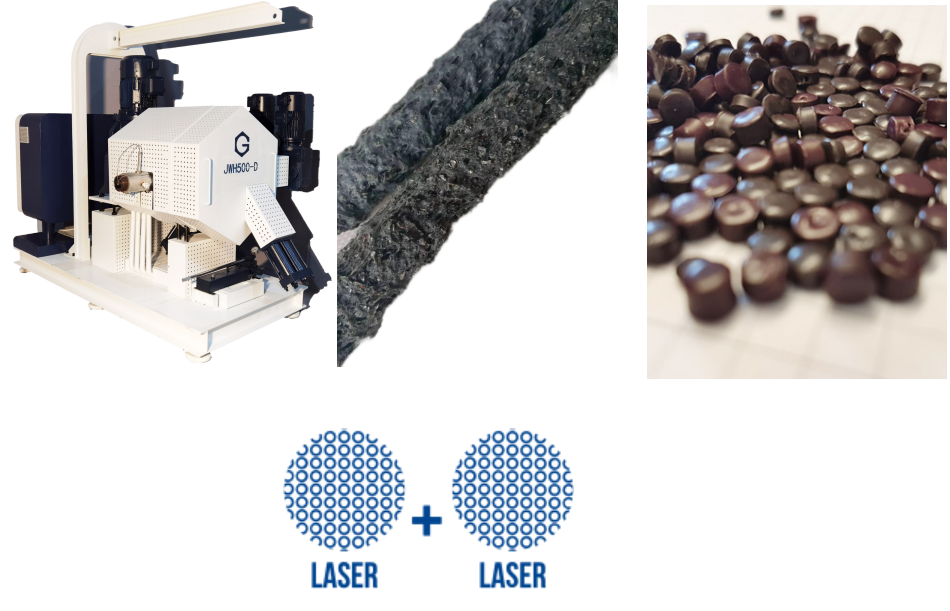
Water cooling strand cutting system
The system includes a cooling tank, a strong wind dryer, and the cold water tank is for cooling the plastic strip drawn from the extruder.
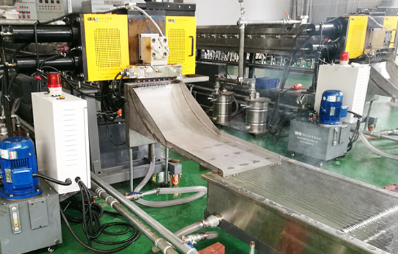
HMI control system
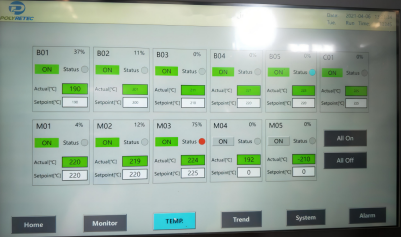
Customer Cases
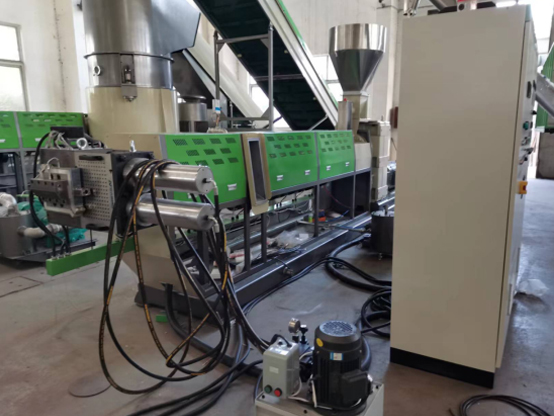
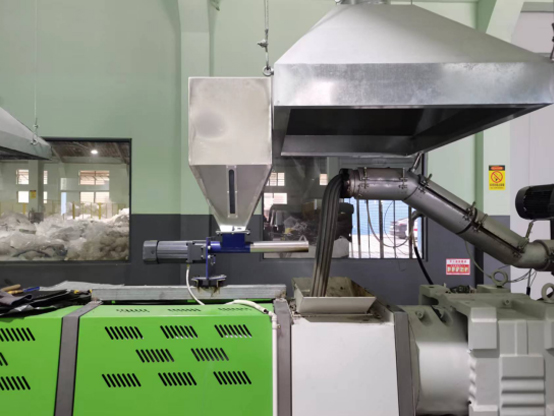
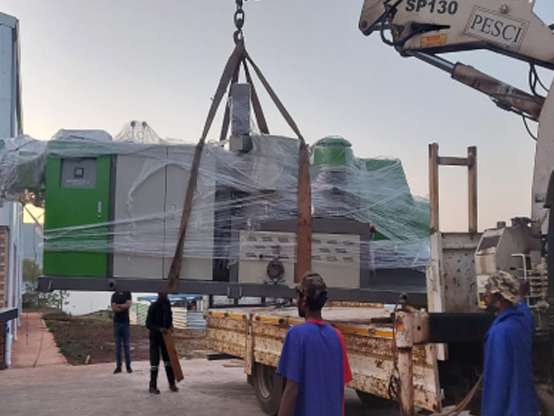
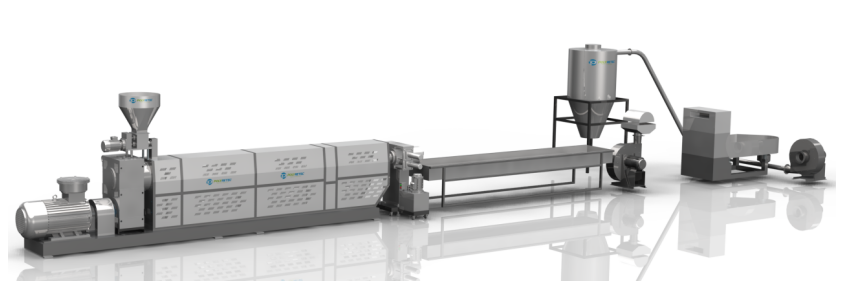
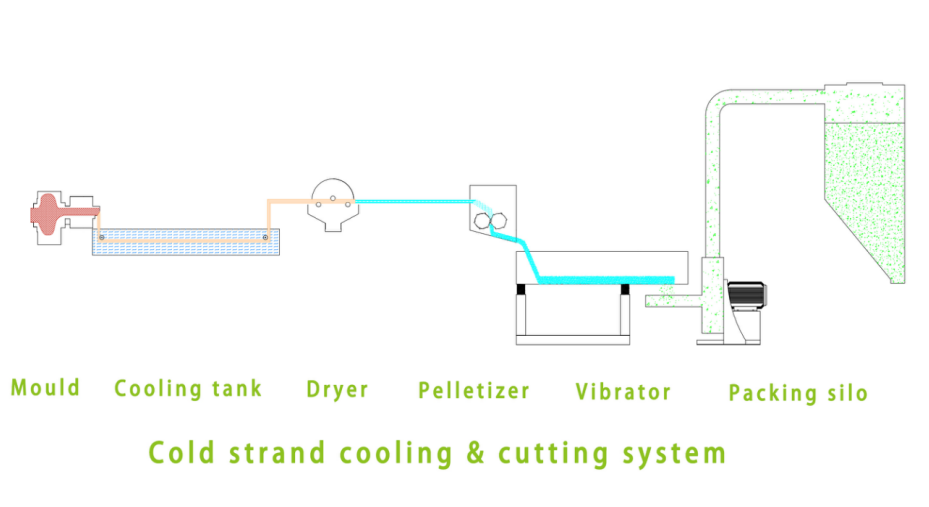
