

Perfect recycling equipment that combines crushing, extrusion and pelletizing in the same machine
The non-woven two-stage plastic granulator is to recycle waste, waste, scrap, inferior products, polyester fiber fabrics, nylon fibers and other non-woven fabrics, polyester fiber fabrics, and nylon fibers, so that the waste plastics can be recycled. The non-woven pelletizing machine completes feeding, crushing, conveying, and pelletizing at one time. The extruder can choose vent or no vent according to the characteristics of the material. The pelletizing method adopts stretch pelletizing, single-board duplex Position screen changer, no downtime, large filtering area.

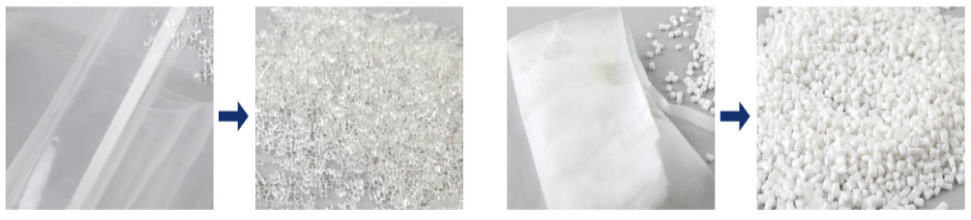
Model | PTCS80-100 | PTCS100-120 | PTCS130-150 | PTCS150-180 | PTCS185-200 |
Screw Diameter (mm) | 80mm&100mm | 100mm&120mm | 130mm&150mm | 150mm&180mm | 185mm&200mm |
l/d | 18-42 | ||||
Spinning Speed (rpm) | 10-150 | ||||
Capacity(kg/hr) | 150-250 | 200-350 | 450-600 | 600-700 | 800-1200 |

Model | PTCS 3 in 1 Plastic Recycling Machine |
Final Product | Plastic pellets |
Structure | Conveyor belt, crushing cylinder, extruder 1, extruder 2, pelletizing unit, water cooling unit, drying unit and storage cylinder, degassing unit, filter unit |
Raw Material | HDPE, LDPE, LLDPE, PP, BOPP, CPP, OPP,PET |
Capacity | 100kg ~ 1200kg/hr |
Feeding System | Belt conveyor, clamp wheel set (optional) |
Screw Diameter | 80~185mm(customized) |
Screw length to diameter ratio | 30/1, 32/1, 34/1, 36/1 (customized) |
Scew Material | 38 chromium molybdenum aluminum or bimetal |
Degassing hole | Double degassing hole, single degassing hole or no degassing hole (customized) |
Filtering system | Double cylinder filtration |
Pelletizing Method | Strand Pelletizing |
Cooling Method | Water Cooling |
Voltage | Customized(for example: US 480V 60Hz,Mexico 440V/220V 60Hz,Saudi Arabia 380V 60Hz,Nigeria 415V 50Hz) |
Options | Metal detector (S+S Germany), wheel set, color master batch and additive meter, centrifugal dehydrator |
Delivery Date | It takes 50~70 days to customize the machine. |
Warranty | 1 Year |
After-sale Service | Engineers can be dispatched to customers' overseas factories to assist in machine installation |
Feeding unit 1
Belt conveyor unit: The recycled waste can be directly placed on the conveyor belt to facilitate feeding, and the conveyor belt controls the feeding rate with ampere quantification

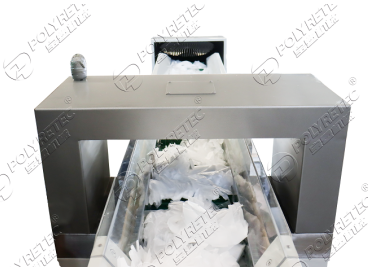
Feeding unit 2
Clamping wheel set: It can be matched with a belt conveyor unit to feed the entire roll of film on the rack at the same time. Cutting compaction system Equipped with a precise temperature control and cutting system to ensure that the semi-molten plastic can quickly and stably enter the extrusion system for mixing

Degassing system
The double-degassing hole of the extruder can release more ink and moisture in the material to improve the quality of the final product.
Filter system
The double-piston filter system has twice as larger than the general plate filter. This filter system can increase the efficiency and reduce the frequency of replacing the filter. Besides, the design of the double flow path allows the machine to keep operating in the process of replacing, to improve the total capacity and reduce waste.
Pelletizing unit-Cold Strand pelletizing system
The cold strand pelletizing system includes a cooling water tank, strong wind dryer and pelletizer. The cooling water tank is used to cool the plastic strips drawn from the extruder.
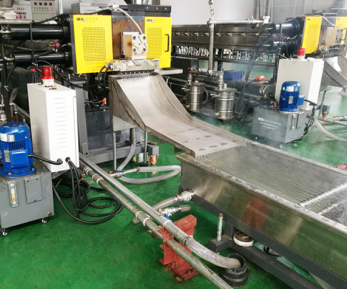
Product
The recycled granules can be used directly into the film-blowing machine or the pipe extruder line again.
Customer installation examples
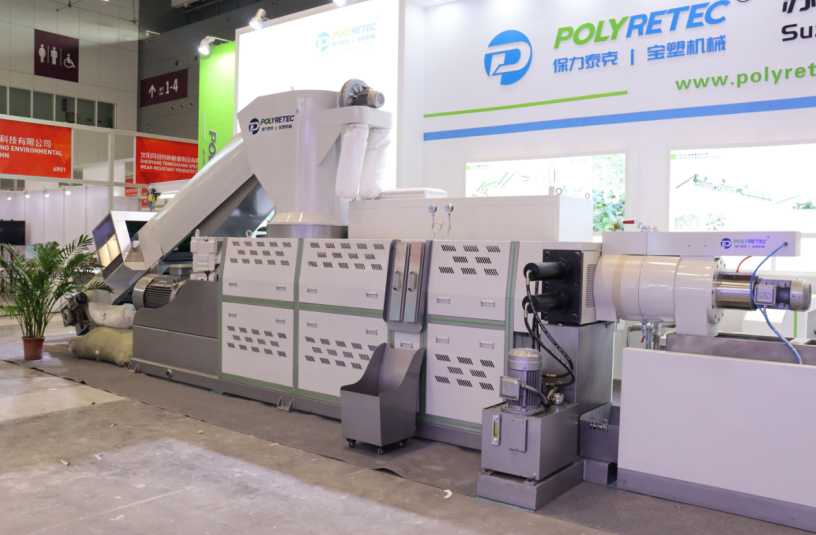
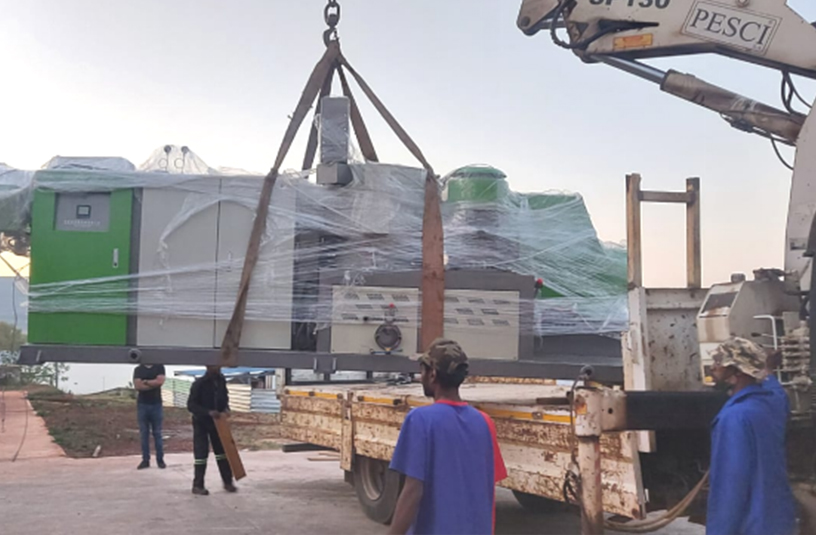