Model | PTCS80 | PTCS100 | PTCS130 | PTCS150 | PTCS185 |
Screw diameter (mm) | 80 | 100 | 130 | 150 | 185 |
L/D | 18-42 | ||||
Rotating speed (rpm) | 10-150 | ||||
Output (KG/h) | 120-220 | 160-280 | 360-480 | 480-750 | 700-1020 |
Power Consumption (kw/h) | 90 | 130 | 220 | 270 | 366 |
Manual | 1-2 | 1-2 | 2-3 | 2-3 | 2-4 |

PTCS High-efficiency Packaging Film Recycling Equipment
Perfect recycling equipment that combines crushing, extrusion and pelletizing in the same machine
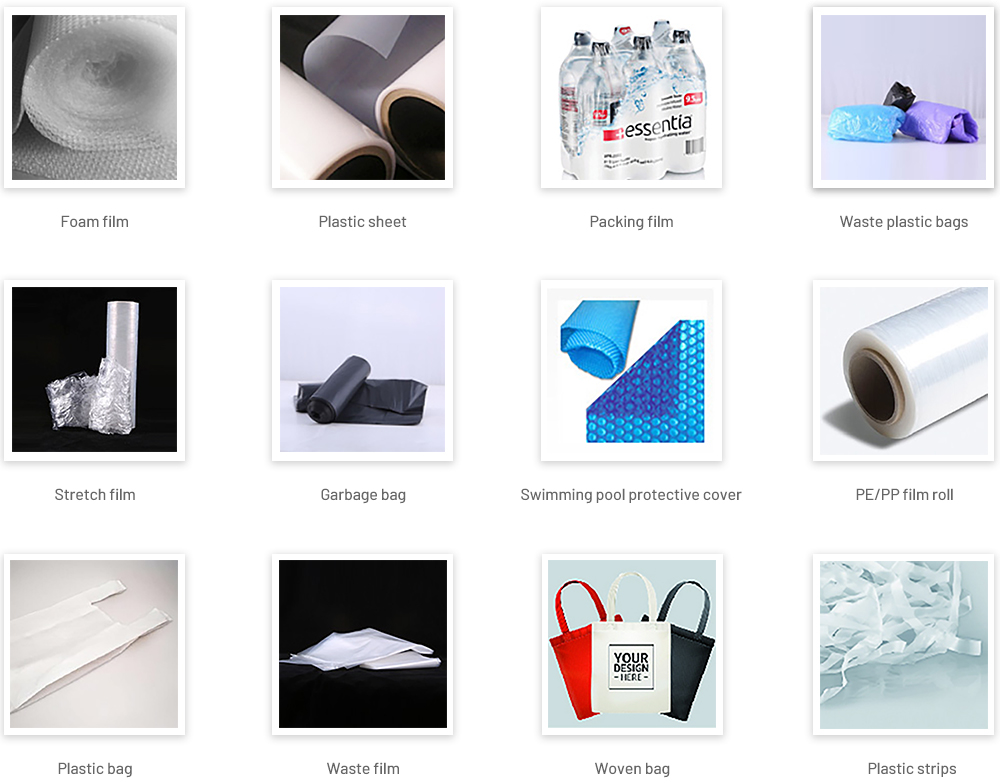


Model | PTCS Three-in-one plastic recycling machine |
Final product | Plastic pellets |
Recycling machine structure | Conveyor belt, crusher, extruder, pelletizing unit, water cooling unit, drying unit and storage drum, degassing unit, filter unit |
Recyclable materials | HDPE, LDPE, LLDPE, PP, BOPP, CPP, OPP, PA, PC, PS, PU, EPS |
Capacity | 100-1200/hr |
Feeding system | Belt conveyor, clamp wheel set (optional) |
Screw diameter | 65~180mm(customized) |
Screw length to diameter ratio | 30/1, 32/1, 34/1, 36/1 (customized) |
Screw material | 38CrMoAl Or bimetal |
Degassing hole | Double degassing hole, single degassing hole or no degassing hole (customized) |
Filtering system | Double-cylinder filtration |
Pellet type | Hot die-cutting type (water-ring cutting) |
Cooling method | Water cooling |
Voltage | Customization (for example: 480V 60Hz in the United States, 440V/220V 60Hz in Mexico, 380V 60Hz in Saudi Arabia, 415V 50Hz in Nigeria) |
Optional accessories | Metal detector (S+S Germany), wheel set, color master batch and additive meter, centrifugal dehydrator |
Delivery date | It takes 50~70 days to customize the machine. |
Warranty | One year |
After-sales service | Engineers can be dispatched to customers' overseas factories to assist in machine installation |

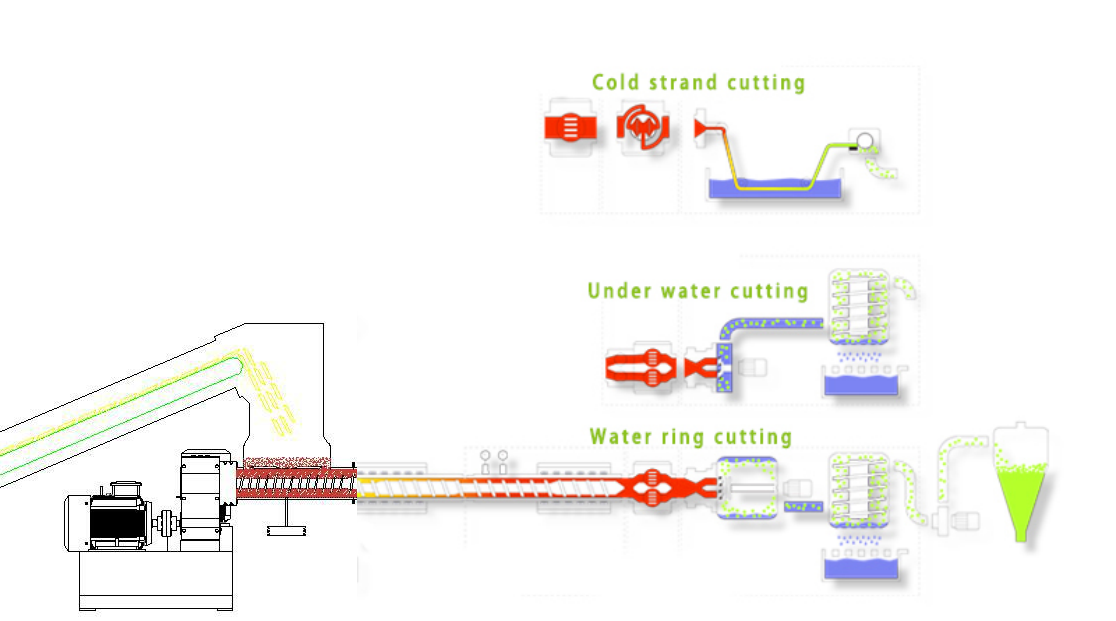

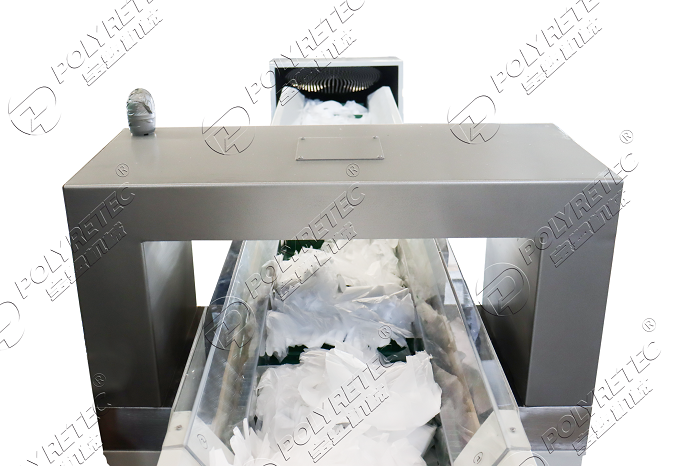
Clamping wheel set: It can be matched with a belt conveyor unit to feed the entire roll of film on the rack at the same time.
Cutting compaction system
Equipped with a precise temperature control and cutting system to ensure that the semi-molten plastic can quickly and stably enter the extrusion system for mixing and fusion.
Degassing hole
The double degassing hole design of the extruder can release more ink and water vapour in the recycled material to improve the quality of the final product.
Filter screen change system
The double-column screen changing system has a filter area twice as large as the general pallet screen changing system. This screen changing system can improve filtration efficiency and reduce the number of screen changes. In addition to reducing the number of screen changes, the dual-channel design allows the machine to continue to operate during the screen change process, increasing the overall production capacity of the machine and reducing waste.
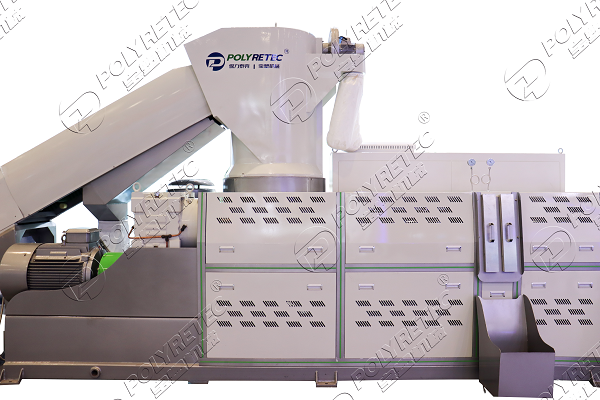

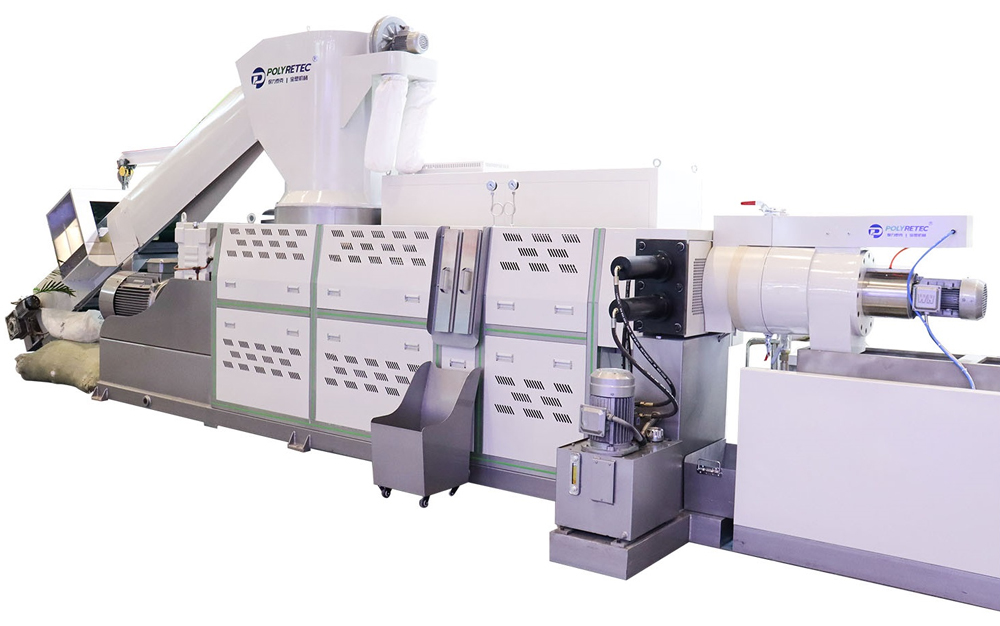
The plastic recycling pelletizing line PTCS manufactured is specially designed to recycle PE (HDPE, LDPE, LLDPE) and PP packaging materials. Except for the clean waste (waste from the production line), the printed surface, the washed waste and the crushed small fragments, all can be recycled by PTCS.
Applicable waste materials include: plastic bag factory waste, food packaging waste, all kinds of plastic bags, shrink film, bale film, agricultural film, PE&PS foam material, disposable tableware, PP wire drawing, woven bag, space bag and The crushed hollow molding and injection products can be used for recycling and pelletizing
1. Recycled clean plastic once-waste from plastic production plants Plastic production plants (blowing factories, bag making factories, and printing factories) generate an average of 5% of the total waste output. Recently, because the prices of petroleum and new materials keep rising, the problem of recycling of waste materials in plastic factories has gradually attracted attention. Using recycled plastic materials to make products again can greatly reduce the cost of purchasing new materials.
Recycling the waste produced by the production line (for example: defective film rolls, cutting ears in the bag making process), the quality of the recycled materials can be up to 98% of the new materials. Many manufacturers currently choose to use primary recycled waste to produce products, and the quality of the products produced is quite close to the products made from new materials. This method can save the cost of using raw materials and increase the market value of the product.
2. Secondary recycling waste-washing waste, plastic particles with trace impurities In response to the needs of different customer groups, PTCS machines can also be used to recycle waste after washing (waste plastic film, agricultural film, cover film for construction projects...). The heat energy generated by the rotation in the PTCS crushing process can be used to heat the waste material after washing and take away the excess water in the material. In the part of the extruder, double degassing holes can release water and printing ink again. The plastic pellets produced by washing raw materials are mostly used to reproduce plastic films used to make garbage bags, engineering films, covering cloth, and to produce water pipes. The PTCS machine can be additionally equipped with a masterbatch/additive feeder to change the color of the recovered particles. Plastic particles with trace impurities
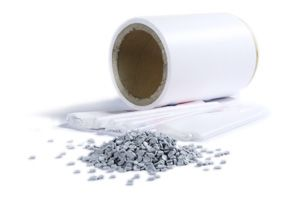
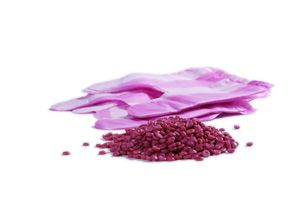
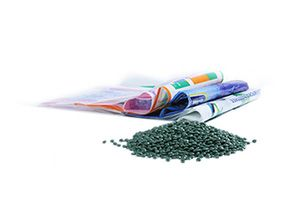

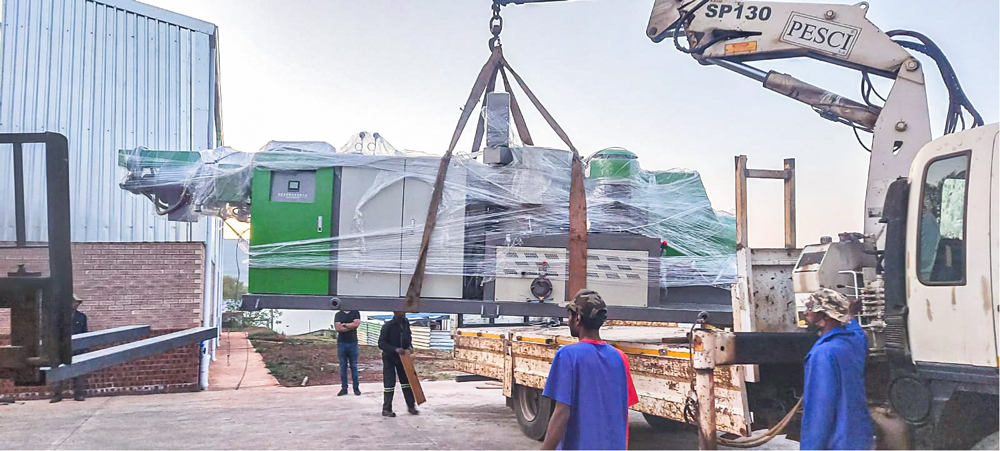
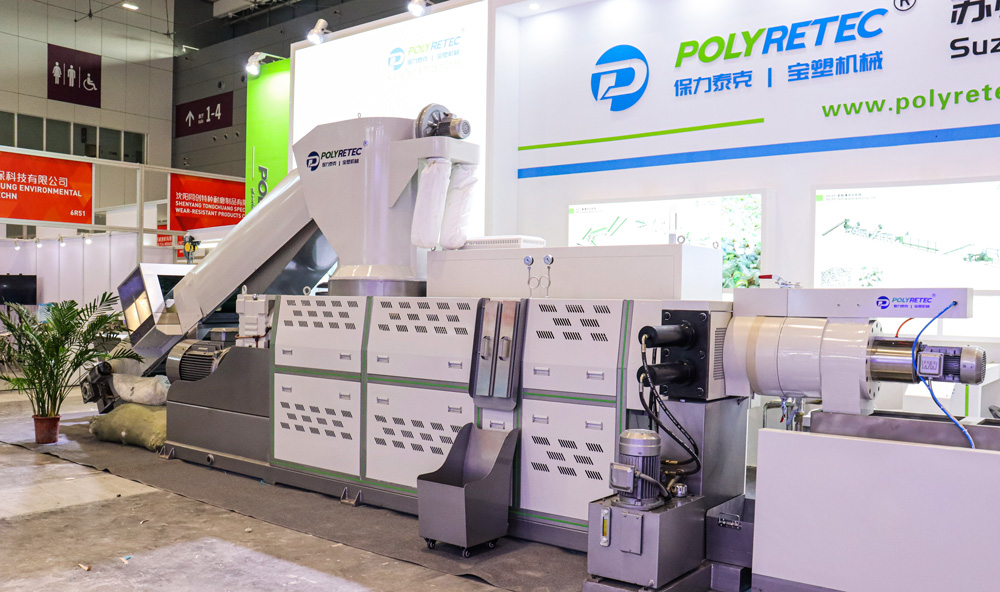

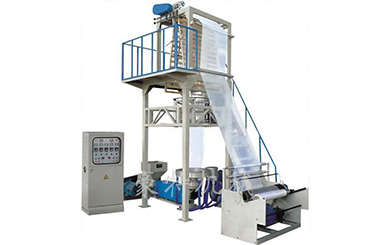
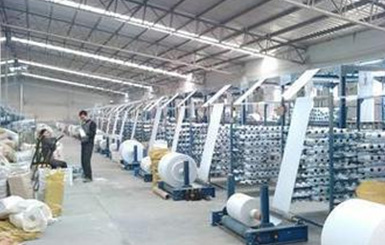
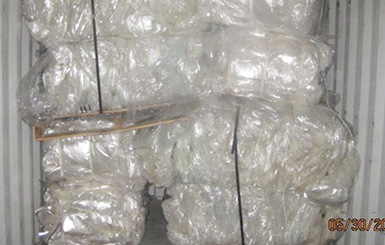
Professional recycling plant
Professional recycling plants buy waste plastic materials everywhere. After washing, these plastic wastes can be made into plastic particles again with PTCS. Recycling plants usually add additional color masterbatch or additives to change the color of the particles and improve the quality.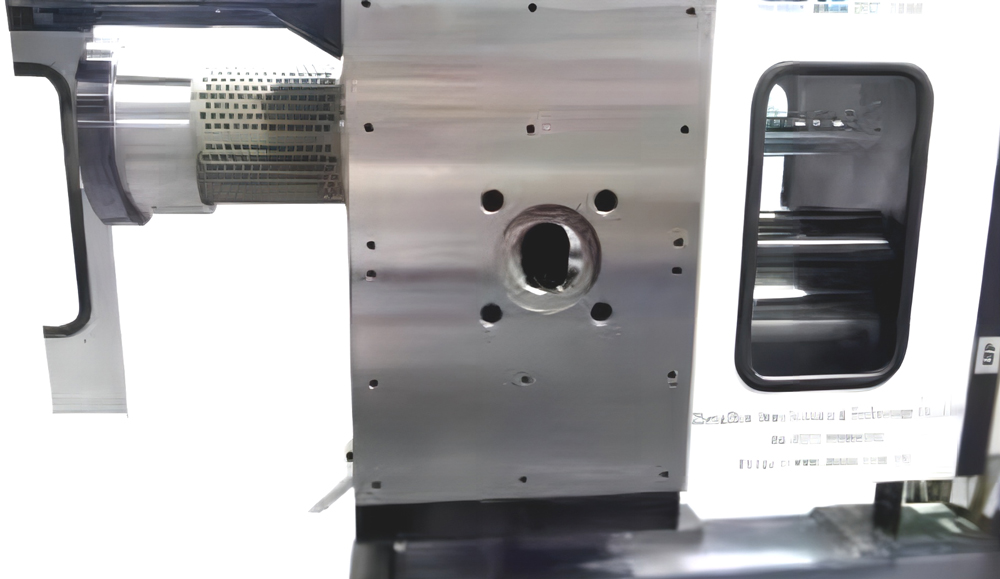
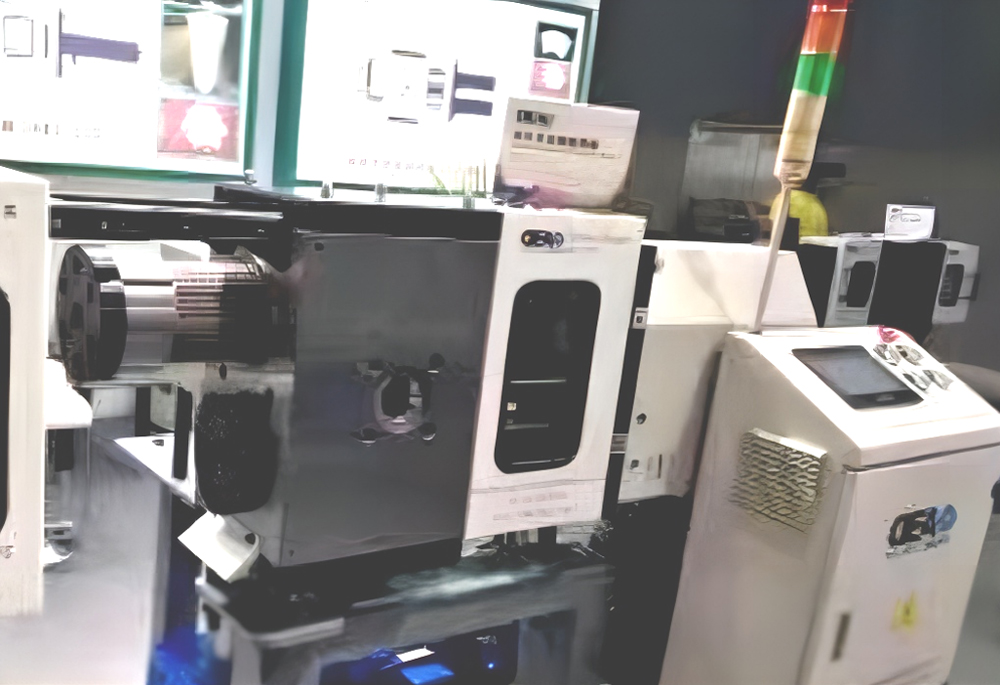
Laser screen changer (optional for post consumer ldpe film )
Applications:
PTJ continuous melt filters are suitable for processing all standard polyolefins and polystyrenes with the exception of PVC、PVDC、EVA; they are designed to remove foreign particles such as paper, aluminum, wood, elastomers (rubber, silicone) or high-melting polymer composites from heavily contaminated materials.
Examples:
Processing material | contamination | Contamination by weight % | Filtration fineness | Waste contamination% | Material losses % |
PE | paper | 5 | 30-120mesh | 58-67 | 3-4 |
PPHDPE | PET | 4 | 57-66 | 2-3 | |
PS | aluminum | 3-4 | 57-60 | 2-3 | |
PP | rubber, silicone | 2-3 | 55-60 | 1-2 | |
PE、PP | composite | 0.5 | 55-65 | 0.3-0.4 |
Technical data
model | PTJ300 | PTJ400-D | PTJ500-D |
Filter diameter in mm | 1X300mm | 2X400mm | 2X500mm |
Filter area in cm2 | 575cm² | 2112cm² | 3472cm² |
Filtration fineness | 120-600μm 30-120Mesh | ||
Maximum operating pressure in bar | 250bar | 250bar | 250bar |
Number of heating zones | 4 | 5 | 6 |
Installed heating capacity in KW | 12 | 28 | 42 |
Engine power in KW | 3.0 | 5.5 | 11.0 |
Motor power discharge screw in KW | 1.5 | 2X1.5 | 2X2.2 |
Throughput capacity in kg/h | 300-500Kg | 500-1200Kg | 1000-2000Kg |
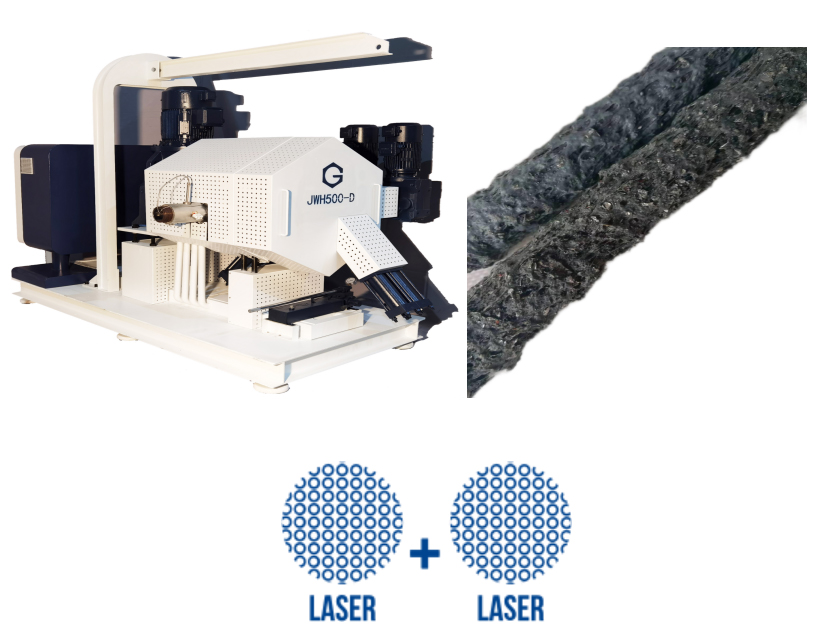
With two independent internal filter rooms and two independent unloading valves
Pelletizing unit
The hot die pelletizing system can immediately pelletize the melted plastic material after extrusion. Immediately after cutting the pellets, it enters the water ring for cooling. The particle shape and size are average, conducive to re-production in various extruders and injection molding machines.
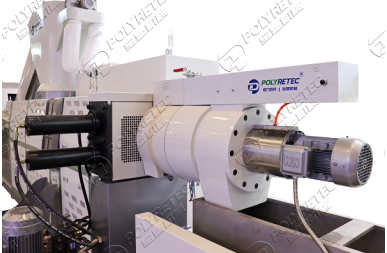
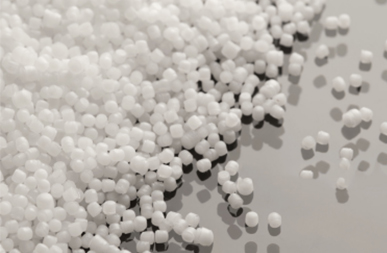