Pesticides are agricultural chemicals used to prevent pests and diseases and regulate plant growth. They are widely used in agriculture, forestry and animal husbandry production, environmental and household hygiene to prevent pests and epidemics, and industrial products to prevent mould and moths. There are many kinds of pesticides, which can be divided into insecticides, acaricides, rodenticides, nematicides, plant growth regulators, etc., according to their uses. According to the bottle material, it is divided into three categories: PET bottles, pure HDPE bottles and bottles with barrier layers. Many pesticide bottles are produced in farming every year. Where are these pesticide bottles processed? POLYTEC is a manufacturer specializing in plastic recycling solutions and equipment manufacturing. Based on the suggestions and feedback from new and old customers, the company has a mature process. They are mainly used for processing PET/HDPE compound pesticide bottles, chemical solvents and other bottle plastics for cleaning, recycling and processing. Regarding the recycling, crushing and washing of agricultural medicine bottles. Because of pesticide residues in pesticide bottles, it is necessary to handle the pesticide residues properly and further deal with wastewater discharges. According to the different quality requirements of customers on the final product, a complete set of washing recycling lines is equipped to make it recyclable without pollution and energy saving.

Plastic film/agricultural film/greenhouse film/tobacco film, etc.: Unweathered LDPE polyethene film (raw materials exposed in the field for more than three years have no actual reuse value) Plastic film/agricultural film/greenhouse film/tobacco film, etc.: Unweathered LDPE polyethene film (raw materials exposed in the field for more than three years have no actual reuse value); Impurities: 1. Soil and sand; (usually the proportion ranges from 40% to 70%, and the majority is soil) 2. Plant straw, roots and leaves. (The proportion is uncertain, depending on the recycling method and region) Sewage components: mainly mud water, sedimentation at the bottom, a small amount of plastic LDPE powder floats (approximately 0.003% by weight) Treatment requirements: Direct discharge after four-stage filtration and sedimentation. The discharge standard is GB3838 industrial grade 3.

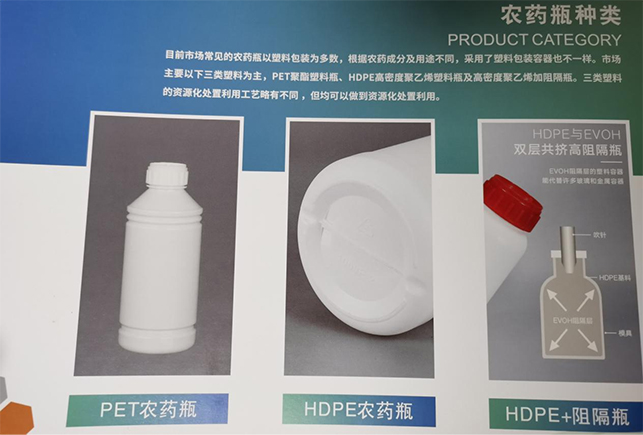
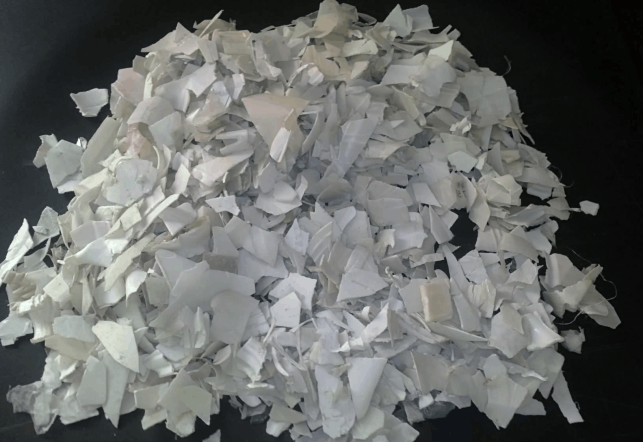

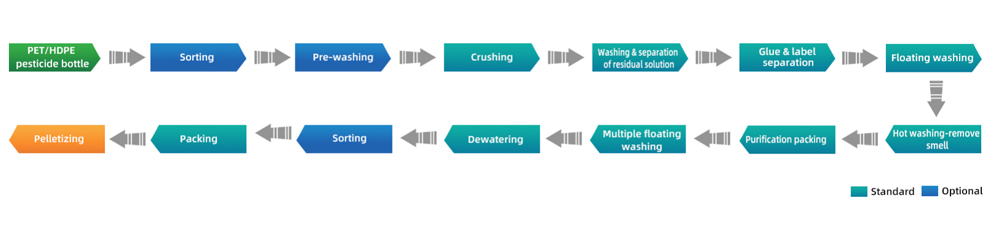

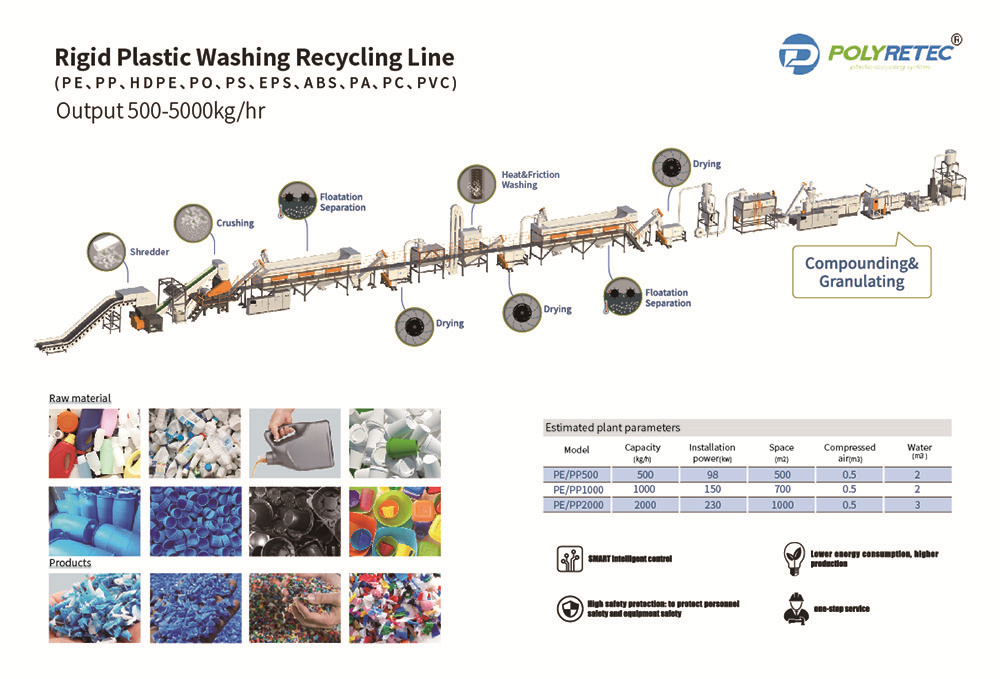
This recycling line is mainly used to process medical waste (infusion bottles, infusion bags), PET/PE composite pesticide bottles, chemical solvents and other bottle plastics for cleaning, recycling, processing and reuse。 Regarding the recycling, crushing and washing of pesticide bottles, our company has a wealth of experience. Because pesticide bottles contain pesticide residues, they need to properly handle the pesticide residues and further deal with the discharge. According to the different quality requirements of customers on the final product, a complete set of washing recycling lines is equipped to make it recyclable and reused efficiently, pollution-free and energy-saving. The recycled pesticide bottles (mainly self-adhesive labelling bottles and PE tape labelling bottles) first enter the selection conveyor for sorting, and the selected PET bottles enter the crusher for crushing treatment. While crushing, some part of the label paper will fall off from the bottle body, and the crushed bottle flakes will enter the vertical washing machine for centrifugal dehydration and washing. The wastewater will be collected separately, and most of the pesticide residue will be collected and discharged from here, Then enter the floating separation tank, the PET bottle flakes are separated from the bottle cap, the bottle cap will flow out from the side to collect, the bottle flakes will enter the next process friction washing machine for intense friction cleaning, to clean away the pesticide residue, also clean the paper label paper of the bottle body (the paper label paper which after soaking is easier to fall off), After friction cleaning, the bottle flakes enter the floating tank for washing. After rinsing, they are automatically sent to the vertical dehydrator for dehydration treatment. Finally, the label paper separation unit can be selected according to requirements.
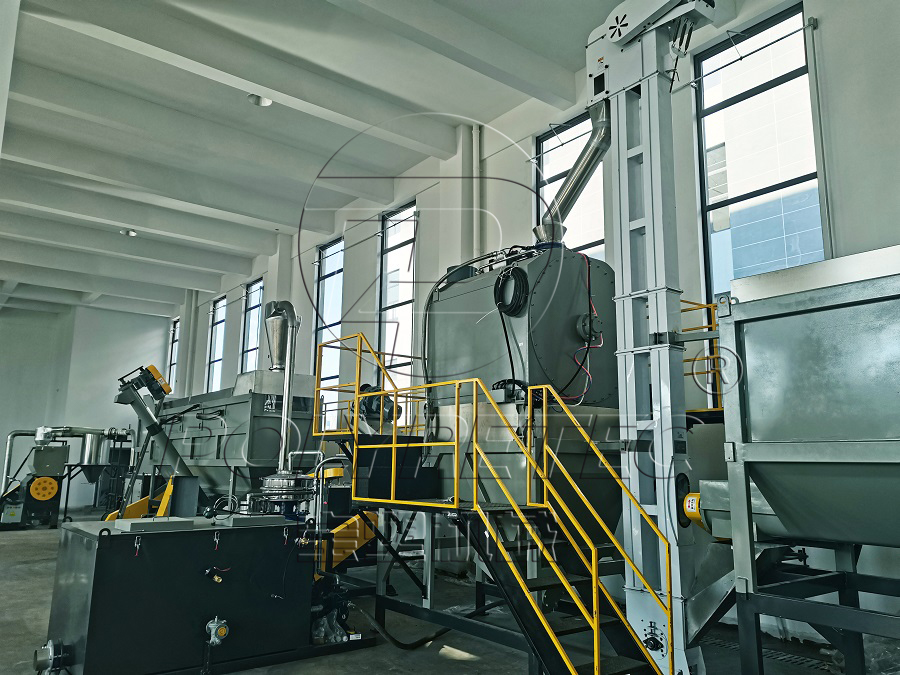
Project parameters
Model | Capacity | Installation power | Space | Steam | Compressed air | water |
PEPP500 | 500kg/h | 98kw | 150m2 | * | 0.5m3 | 2m3 |
PEPP1000 | 1000kg/h | 150kw | 200m2 | * | 0.5m3 | 2m3 |
PEPP2000 | 2000kg/h | 190kw | 300m2 | * | 0.5m3 | 3m3 |
Energy consumption No | Name | Consumption/ton | No | Name | Consumption/ton |
1. | electricity | 50-80kw | 3. | Clean agent (option) | 0-3kg |
2. | Steam (option) | 0-100kg | 4. | water | 0.8-1.5T |
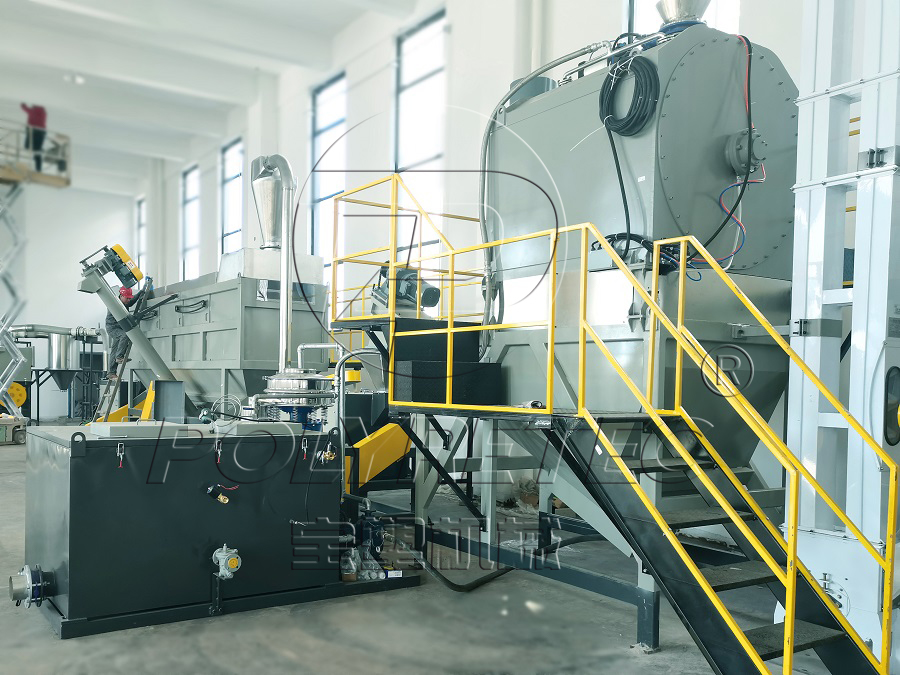
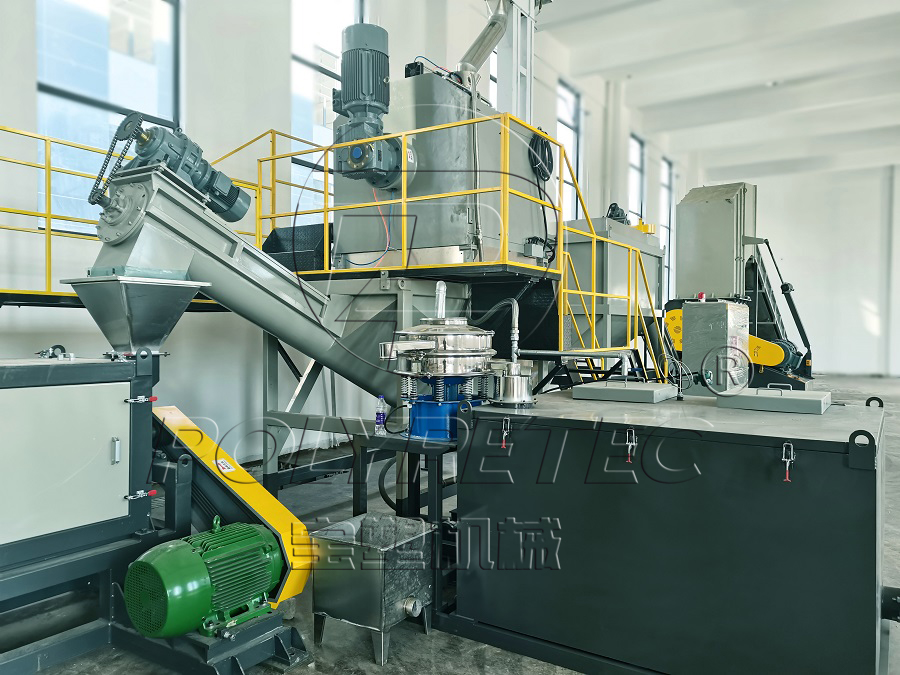
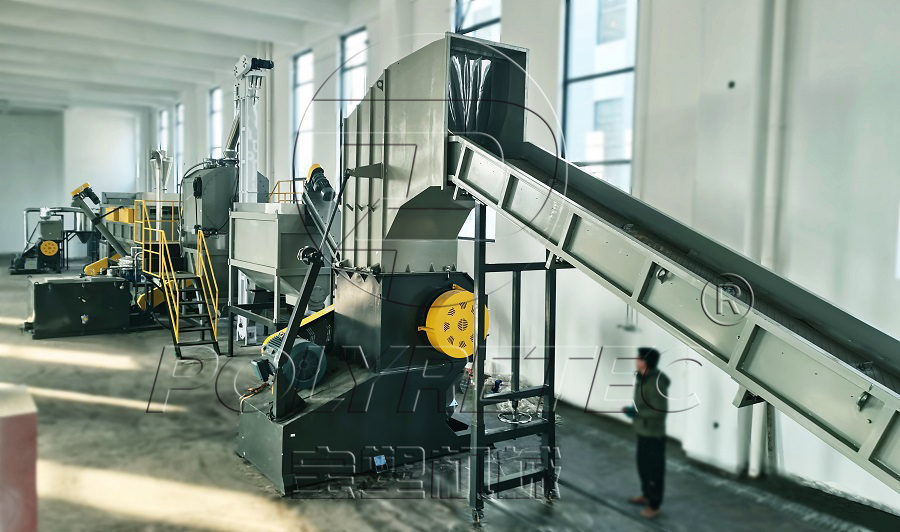