
Model | PTCS80 | PTCS100 | PTCS130 | PTCS150 | PTCS185 |
Screw diameter (mm) | 80 | 100 | 130 | 150 | 185 |
L/D | 18-42 | ||||
Rotating speed (rpm) | 10-150 | ||||
Output (KG/h) | 120-220 | 160-280 | 360-480 | 480-750 | 700-1020 |
Power Consumption (kw/h) | 90 | 130 | 220 | 270 | 366 |
Manual | 1-2 | 1-2 | 2-3 | 2-3 | 2-4 |

Raw materials: pp sacks ,pp bags ,jumbo bags ,bopp packing film,foam film, plastic sheet, telescopic film, waste plastic bag
Perfect recycling equipment that combines crushing, extrusion and pelletizing in the same machine
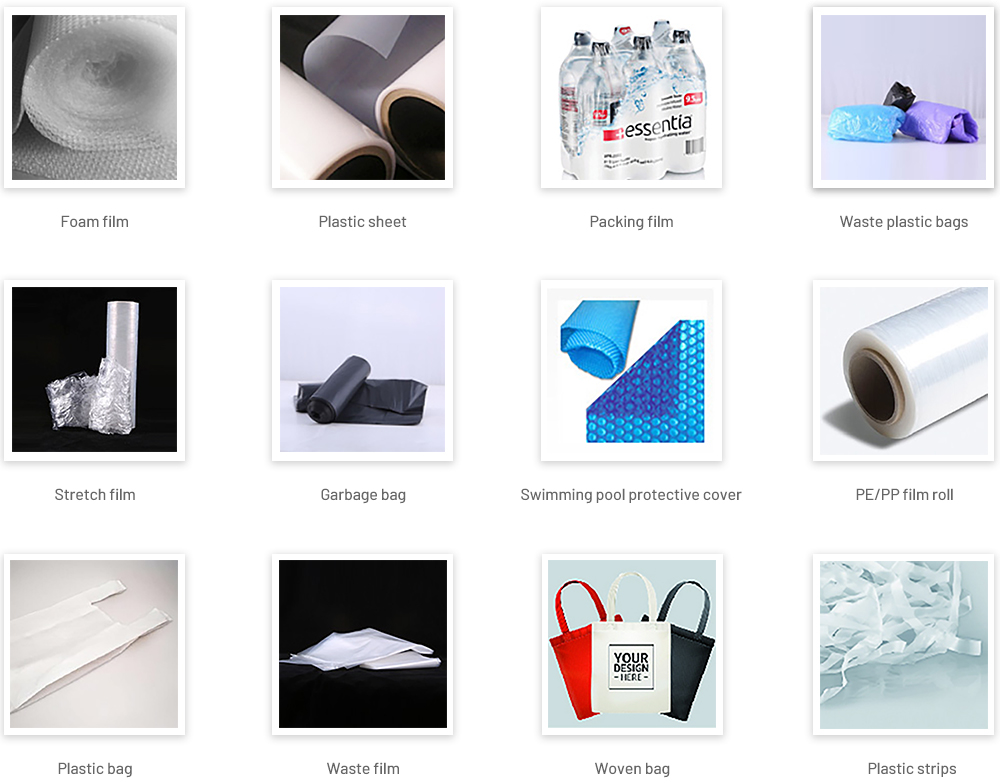


Model | PTCS Three-in-one plastic recycling machine |
Final product | Plastic pellets |
Recycling machine structure | Conveyor belt, crusher, extruder, pelletizing unit, water cooling unit, drying unit and storage drum, degassing unit, filter unit |
Recyclable materials | HDPE, LDPE, LLDPE, PP, BOPP, CPP, OPP, PA, PC, PS, PU, EPS |
Capacity | 100-1200/hr |
Feeding system | Belt conveyor, clamp wheel set (optional) |
Screw diameter | 65~180mm(customized) |
Screw length to diameter ratio | 30/1, 32/1, 34/1, 36/1 (customized) |
Screw material | 38CrMoAl Or bimetal |
Degassing hole | Double degassing hole, single degassing hole or no degassing hole (customized) |
Filtering system | Double-cylinder filtration |
Pellet type | Hot die-cutting type (water-ring cutting) |
Cooling method | Water cooling |
Voltage | Customization (for example: 480V 60Hz in the United States, 440V/220V 60Hz in Mexico, 380V 60Hz in Saudi Arabia, 415V 50Hz in Nigeria) |
Optional accessories | Metal detector (S+S Germany), wheel set, color master batch and additive meter, centrifugal dehydrator |
Delivery date | It takes 50~70 days to customize the machine. |
Warranty | One year |
After-sales service | Engineers can be dispatched to customers' overseas factories to assist in machine installation |

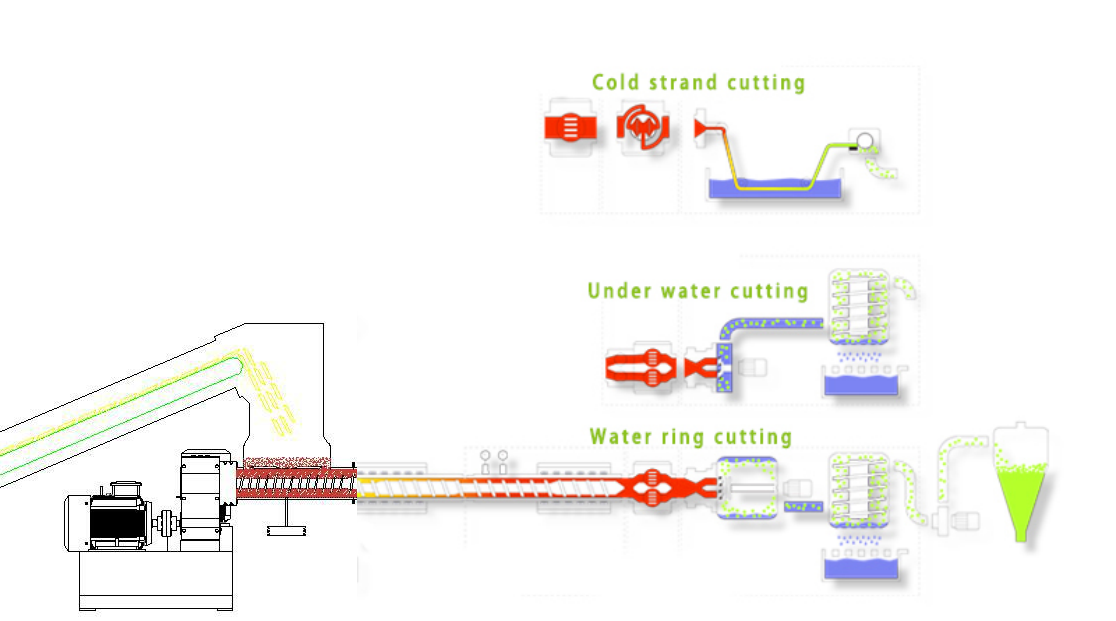

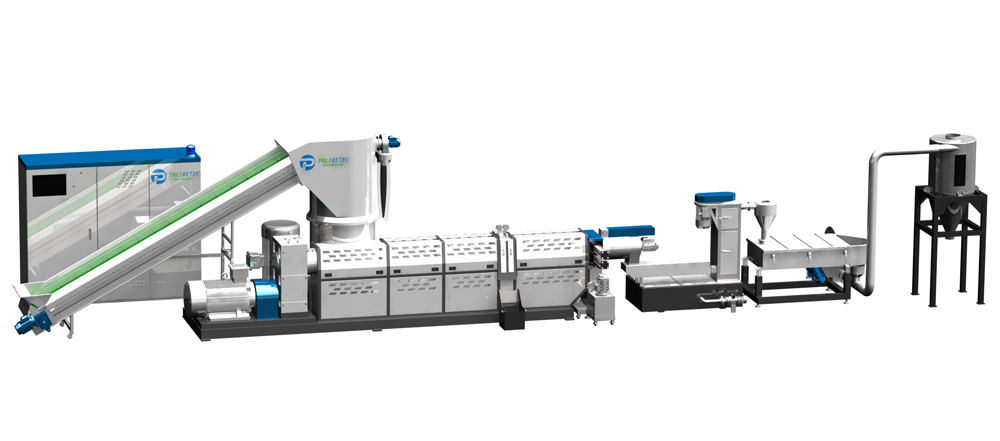
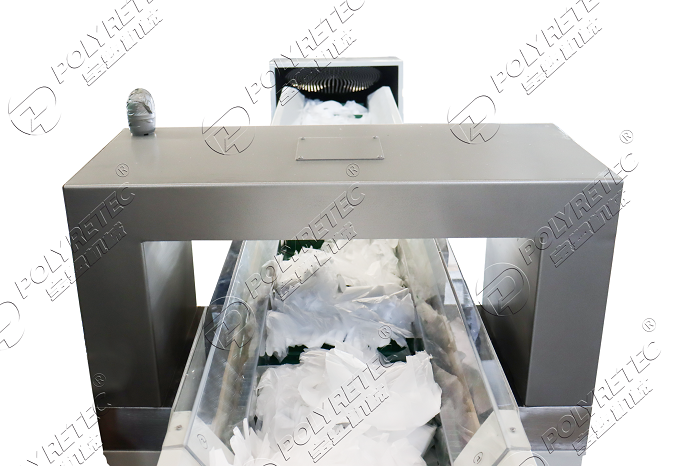
The gripping wheel set can be coupled with a belt conveyor unit to dispense the entire reel of film onto the stand simultaneously.
Cutting compaction system
Furnished with an accurate temp control and cutting mechanism for ensuring that the partially melted plastic can swiftly and consistently enter the blending and merging system.
Degassing hole
The extruder's dual venting orifices aid in the release of increased amounts of ink and water vapor from the reprocessed material, leading to an enhanced final product quality.
Filter screen change system
The dual-column display switching system possesses a filter area that is two times larger than the typical platform display switching system. This switching system can enhance screening effectiveness and decrease the frequency of screen alterations. Furthermore, apart from decreasing the frequency of screen alterations, the double-channel layout permits the machine to remain operational while the screen change is taking place, thereby advancing the machine's overall production capacity and diminishing waste.
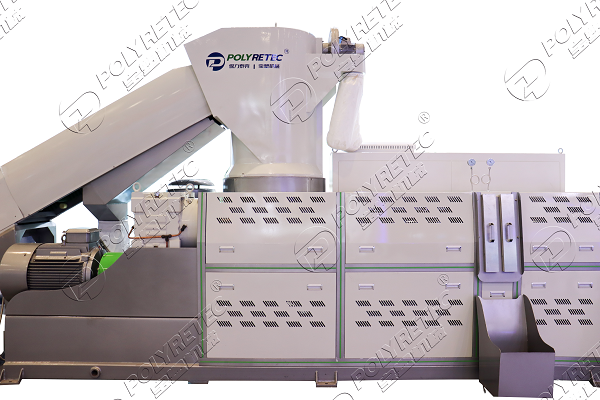
Pelletizing unit
The heated die system swiftly forms pellets with the molten plastic following extrusion. Right after the pellets are cut, they go into the water loop for cooling. The average size and shape of the particles make them suitable for reproduction in different extruders and injection molding machines.
Product The recycled particles of the product can be 100% directly put into the film blowing machine or pipe extruder production line for reuse.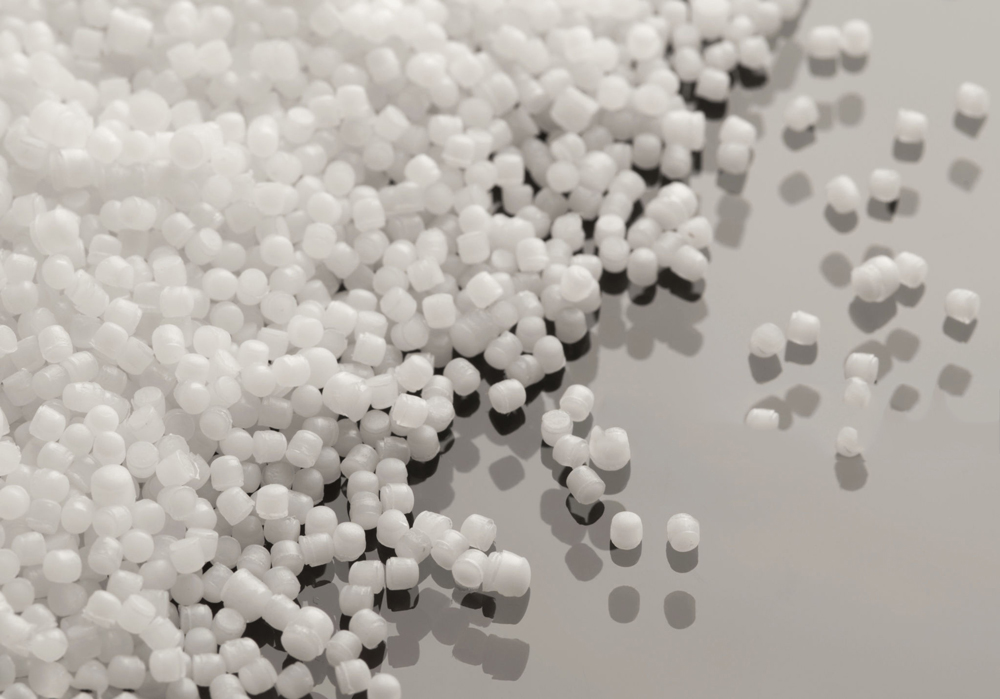

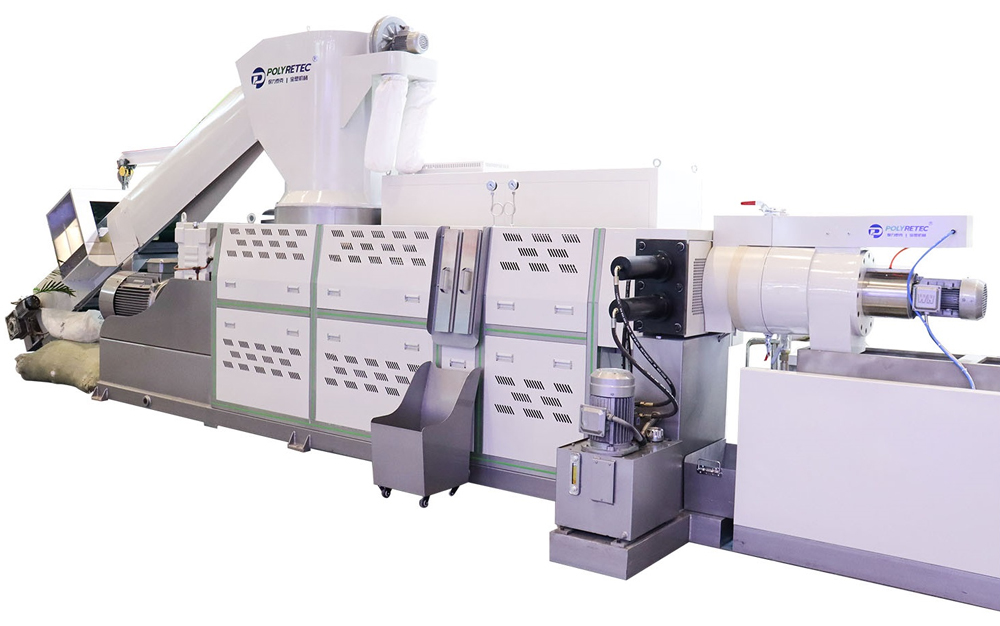
The PTCS plastic recycling pelletizing line is specifically fabricated for the regeneration of PE (HDPE, LDPE, LLDPE) and PP packaging materials. Apart from the unsoiled waste (waste from the production line), the imprinted surface, the cleaned waste, and the shattered tiny fragments, all can be regenerated by PTCS. Eligible waste materials encompass: discarded products from plastic bag manufacturing, waste from food packaging, a wide variety of plastic pouches, contractile film, bundled film, agricultural film, PE&PS foam material, expendable serving items, PP wire drawing, woven pouch, roomy bag, and //The crushed hollow molding and injection products can be employed for regeneration and pelletizing.

1. Recycled clean plastic once-waste from plastic production plants Plastic manufacturing facilities (such as extrusion plants, sack fabrication facilities, and imprinting facilities) produce an average of 5% of the entire refuse yield. Lately, owing to the escalating costs of crude oil and novel components, the matter of recycling of refuse materials in plastic factories has gradually drawn attention. Employing reclaimed plastic materials to fabricate products again can significantly diminish the expense of buying new materials.By reusing the refuse generated by the manufacturing process (for instance: flawed film rolls, trimmings from the sack fabrication process), the caliber of the reused materials can reach up to 98% of the new materials. Numerous producers currently opt to utilize original recycled refuse to craft products, and the caliber of the products produced is quite akin to the products made from new materials. This approach can trim down the expense of utilizing raw materials and heighten the commercial value of the product.
2. Secondary recycling waste-washing waste, plastic particles with trace impurities To address the requirements of diverse customer demographics, PTCS machinery can similarly be employed to reprocess waste post-cleansing (scrap plastic film, farming film, project covering film...). The thermal energy produced by the spinning in the PTCS pulverizing process is capable of heating the cleansed waste material, extracting surplus water. Within the extruder section, twin degassing apertures can once again emit water and print ink. The plastic granules yielded from cleansing raw materials are largely utilized to regenerate plastic film for creating trash bags, construction film, sheathing material, and manufacturing water pipes. Moreover, the PTCS machinery can be furnished with a masterbatch/additive dispenser for altering the hue of the reclaimed particles. Plastic particles containing minute pollutants
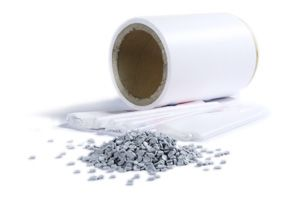
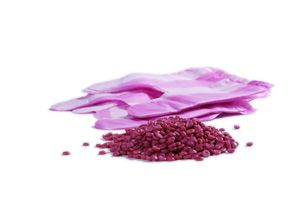
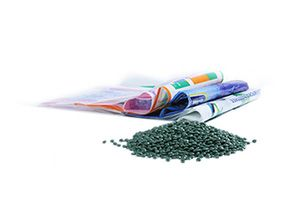

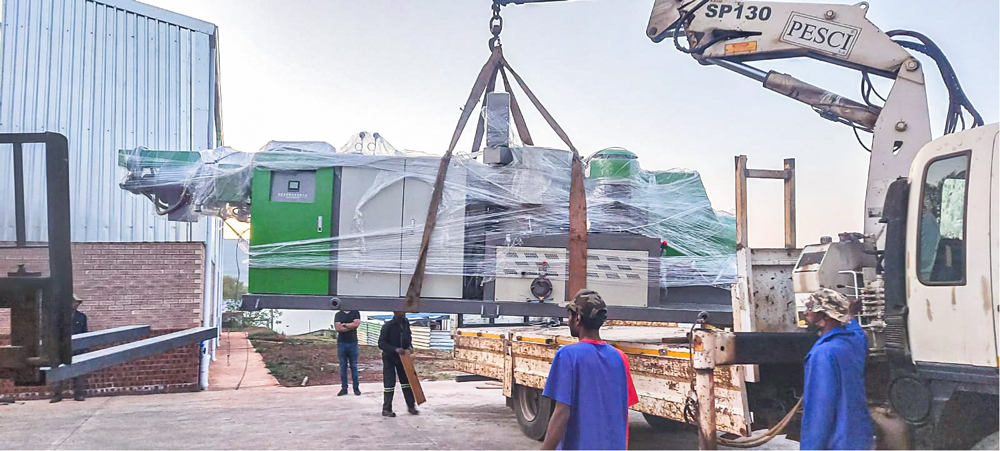
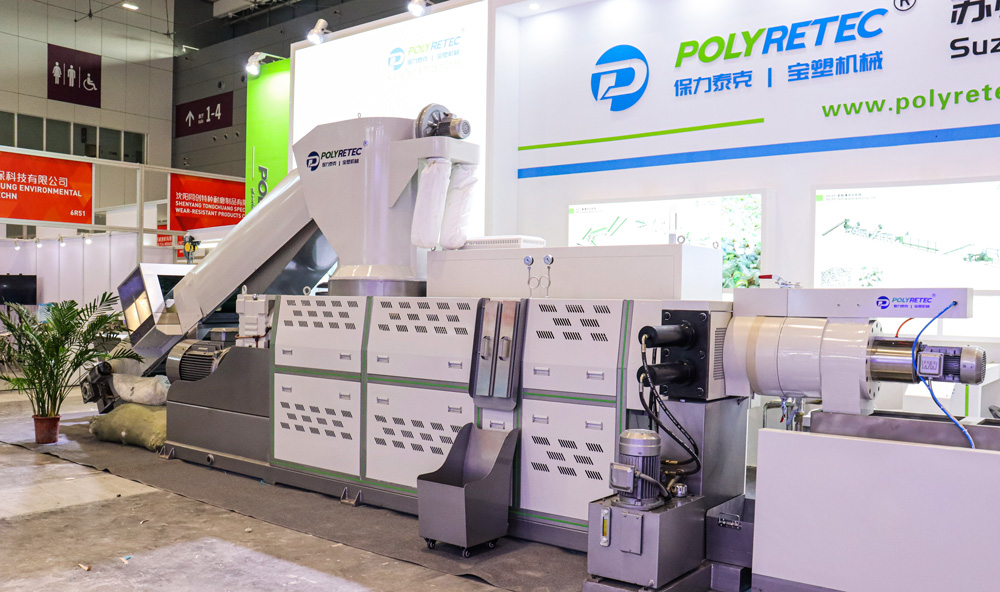

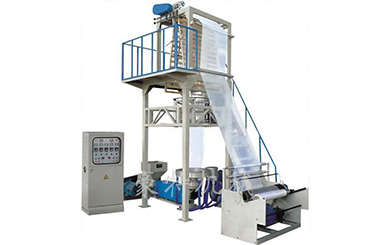
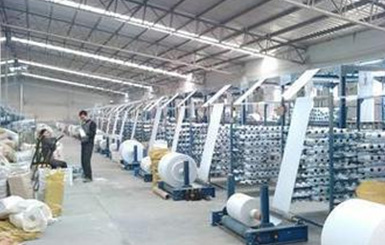
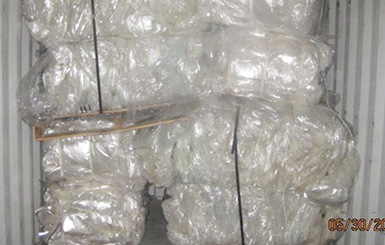
Professional recycling plant
Experienced recycling facilities acquire discarded plastic materials universally. Subsequent to cleaning, these plastic residues can be transformed anew into plastic granules utilizing PTCS. Typically, recycling facilities incorporate supplementary color masterbatch or additives to alter the particles' color and enhance their quality.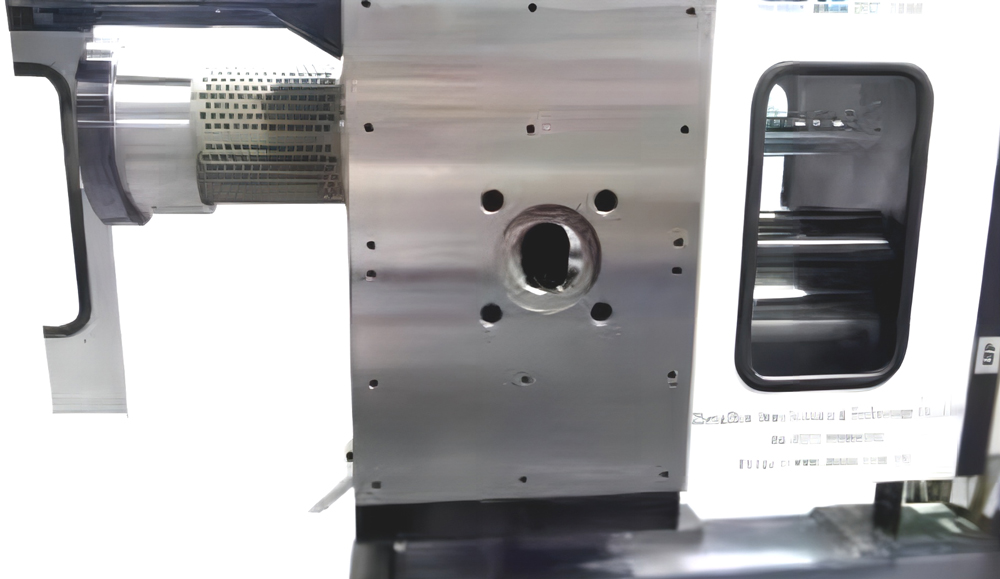
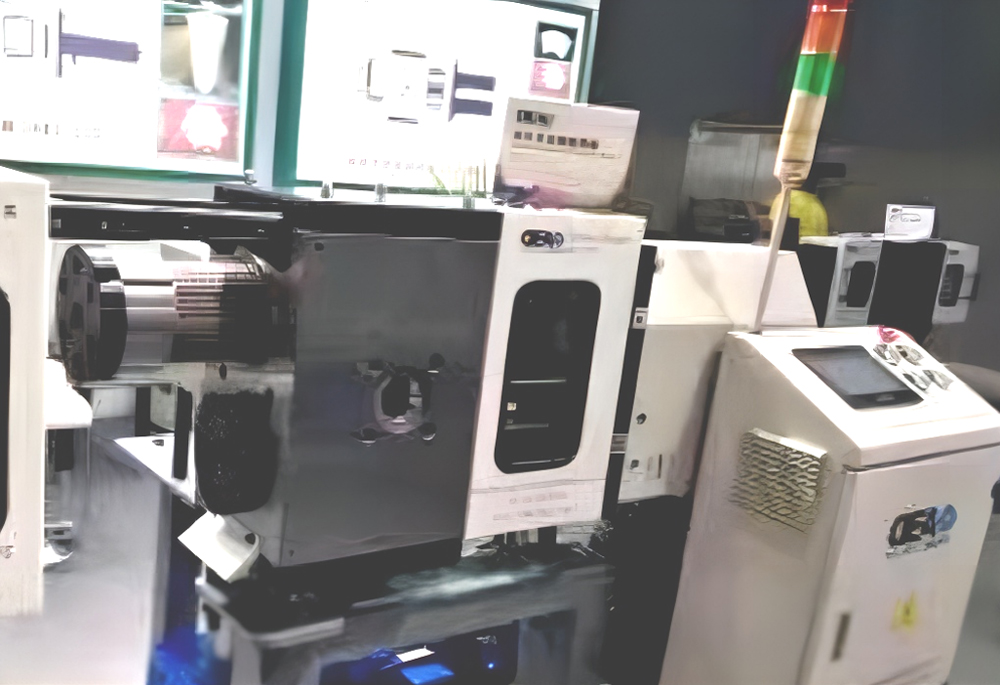
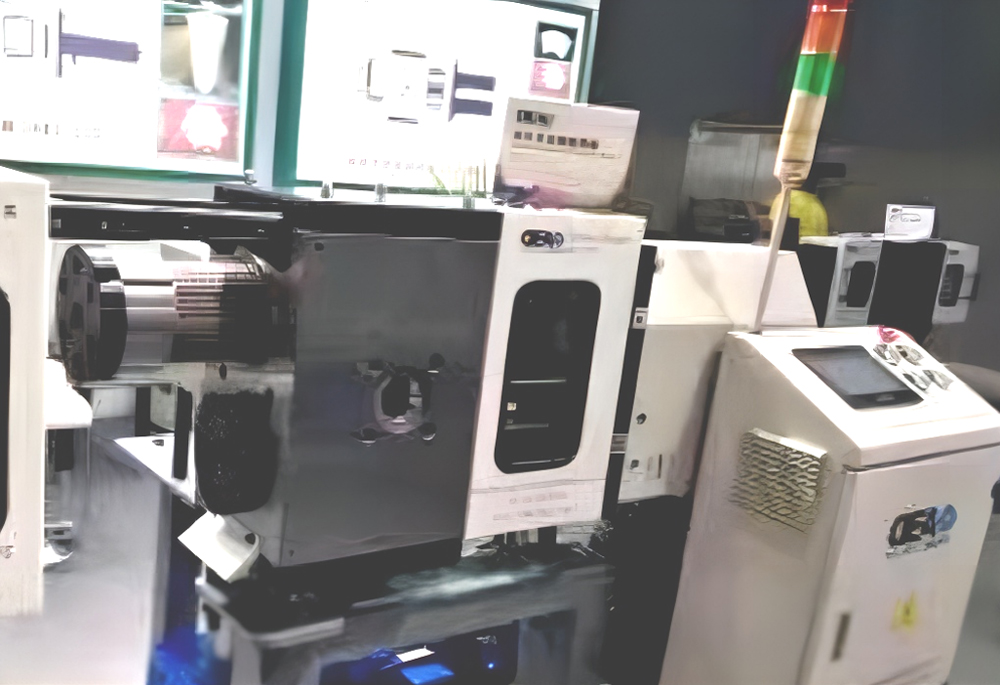